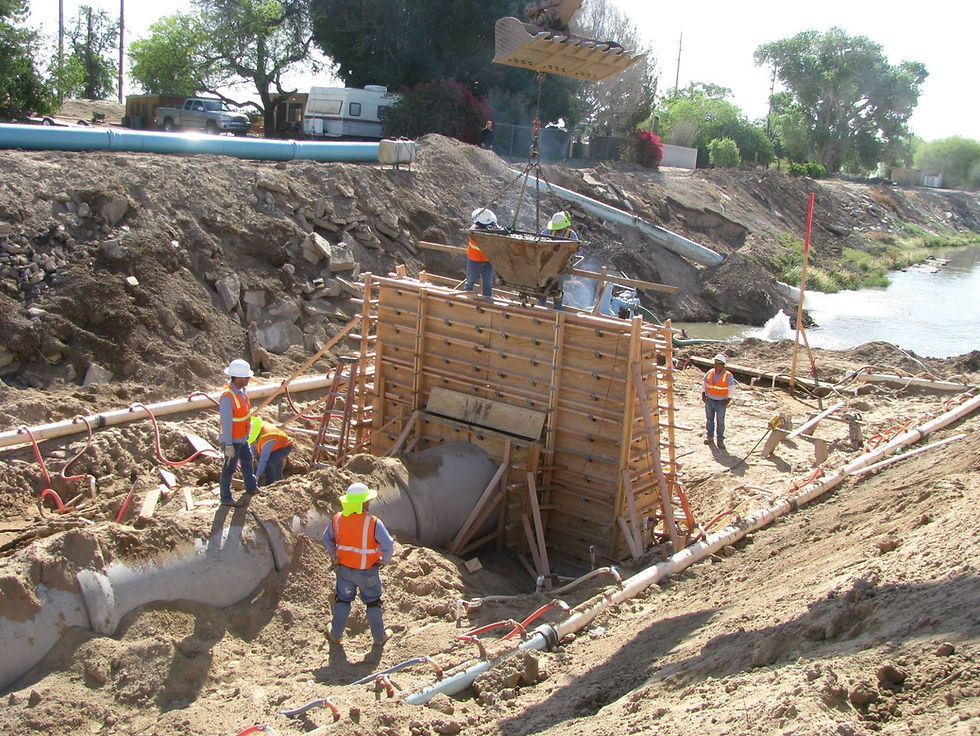
cast in place headwalls
If a precast headwall is not practical for a particular situation, the outlet pipe is too large, or the design is otherwise too complex a headwall will be formed and cast in place instead.
These types of cast in place headwalls provide support and structural integrity, are often larger than precast headwalls, and most commonly installed at either end of a large diameter pipe or box culvert in conjunction with a road or drive passing above.
For a cast in place headwall, a 6-12” layer of porous aggregate bedding is commonly placed in the proposed area(s) of the headwall for access, footing, and structure leveling. A footing is earth cast or formed with lumber often in the shape of a “U” and placed first, typically with rebar reinforcement.

Then the actual primary portion of the headwall is formed with plywood, studs, walers, ties, strongbacks, and bracing. Sometimes manufactured forming systems are used such as steel framed forms with a plastic or composite replaceable form facing material. One side of the wall is formed and oiled, the reinforcement is tied, then the second side of the form is oiled and placed. Typically the culvert pipe, whether round or rectangular, will need to be boxed/formed out inside the wall prior to placing the concrete. This can be a difficult task depending on the size of the pipe, type of forms used, and amount of rebar in the headwall. The alternative to this approach is to place the outlet pipe directly inside the headwall concrete forms and butt it against the inside of the face form and pour around it.

Then the actual primary portion of the headwall is formed with plywood, studs, walers, ties, strongbacks, and bracing. Sometimes manufactured forming systems are used such as steel framed forms with a plastic or composite replaceable form facing material. One side of the wall is formed and oiled, the reinforcement is tied, then the second side of the form is oiled and placed. Typically the culvert pipe, whether round or rectangular, will need to be boxed/formed out inside the wall prior to placing the concrete. This can be a difficult task depending on the size of the pipe, type of forms used, and amount of rebar in the headwall. The alternative to this approach is to place the outlet pipe directly inside the headwall concrete forms and butt it against the inside of the face form and pour around it.
Once the forms are stripped, it is common at a minimum for larger sized honeycombed holes and tie holes to be patched with a mortar or grout mixture to minimize the possibility of moisture getting into the wall and deteriorating the steel and damaging the structure of the wall.
Sometimes the engineer will require that the wall be finished or ‘rubbed’ which basically consists of rubbing the wall with a fine mortar or grout mixture using a burlap cloth or brush. In high visibility areas where an architectural look is desired, sometimes it may be required to ‘sack’ the exposed parts of the newly cast headwall which consists of cleaning and drying the wall then pressure spraying it with a mortar mixture and finishing the surface with a buffing tool. This approach arguably provides the most pleasing architectural look but is often the most costly and resource intensive.
Once the headwall had been placed and has reached acceptable strength, typically 1-3 days for standard concrete mixtures; less for accelerated mixes, the actual culvert pipe is lowered into place within the headwall and grouted around the perimeter pipe/headwall joint. It is common for peel and stick mastic material to be installed on the headwall portion that will receive and support the culvert pipe to minimize water infiltration.