
Finishing concrete is necessary to provide both an aesthetic appearance and to prepare the concrete for long term durability based on its intended future uses. There are many different types of concrete finishes but there are 2 that are used most commonly:
Broom finish


Smooth trowel finish
Exterior concrete typically receives a broom finish to give it a gritty non-slip texture for both foot traffic and vehicle tires. Interior slabs and floors typically receive a smooth troweled finish.
There are many different concrete finishing tools available, following are some of the most commonly used in order of operation:
Straight edge (screed) – A straight edge or ‘screed’ is used to ‘strike off’ the surface of concrete (guided by way of the perimeter forms) after initial placement giving the concrete a rough ‘grade’. Screeds range from 2x lumber, to aluminum units, to engine powered pull units, to laser guided wheeled units.


Powered aluminum hand screed
Mini laser screed tire unit

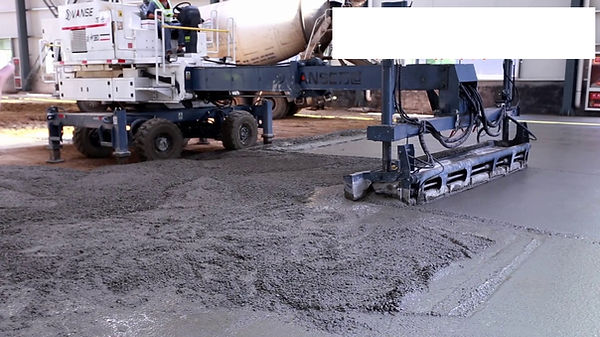
Laser screed with extendable boom
Darby – A darby is a hand held straight edge between 3′ and 8′ long and (on a smaller scale than a straight edge) is used to level localized ridges and to fill voids in the concrete left after screeding and prior to floating. They are often wood or

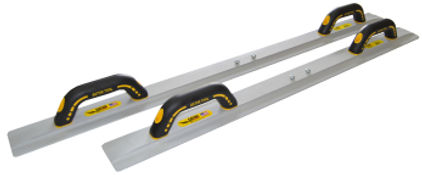

Edgers – An edger is used along the edge of a formed concrete piece to give it a clean radiused, straight, or chamfered edge. It will also slightly compact the concrete along the form making the edges of the concrete more durable. An edger is typically made of steel or aluminum and comes in all sizes and types.
Bull float – A bull float is an attachment which typically goes on the end of a pole which is used to ‘float’ the concrete into place by leveling ridges and filling in low spots left by the screeding process. They also work to embed the larger aggregate particles and bring up cream or paste to the surface to make finishing operations more efficient.
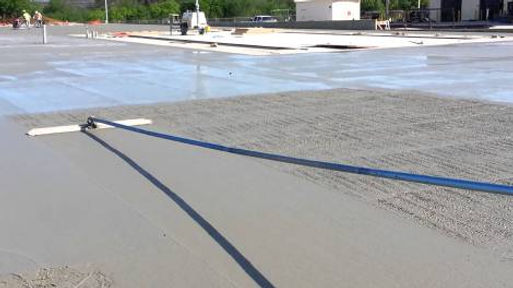

Jointer – A jointer is another hand held concrete finishing tool similar to an edger only it’s used to form aesthetic or contraction joints in a slab of concrete.
Trowel – Troweling concrete provides a dense and smooth concrete surface and can be done by hand or machine. Naturally, machine powered trowel jobs provide greater density and wear resistance because the troweler can apply greater pressure, increasing densification.
The most common 3 types of steel used for trowels are blue, stainless, and high carbon steel. Blue steel trowels are lightweight and flexible while stainless steel trowels will not rust. Trowels commonly range between 8-24″ long by 3-6″ wide.
Walk behind engine powered trowels are used for larger slabs/areas and their engines range from 5-10 horsepower. After the floating operation is complete, hand troweling is commonly done prior to any power troweling to get the hard to reach/finish areas: edges, joints, columns, corners, and walls. This will also address any high spots that the power trowel cannot take care of.
Rideable dual blade power trowels are also available for larger slabs where enough power is needed for a larger area when only a certain window of time is available.
Hand trowel
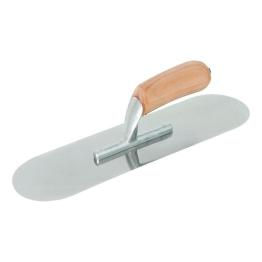

Walk behind power trowel
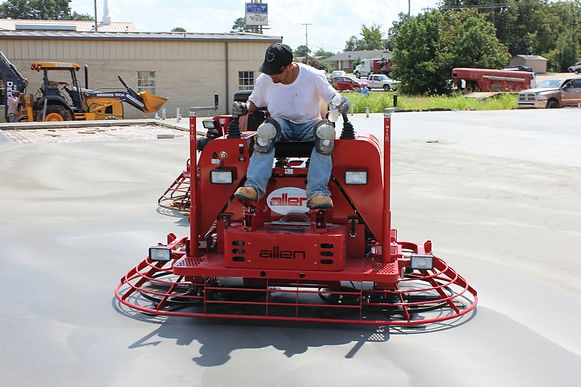
Riding Dual-Blade Power Trowel
Some common size ranges of power trowels are 24″ (mainly for finished building interiors, doorways, corners, etc) and 32-48″ (most common size for medium to large slabs). Power troweling must be done as soon as soon as the strength of the curing concrete will allow, but not so late that the concrete has setup resisting any troweling efforts on the surface. A good rule of thumb is when the surface of the concrete leaves footprints of 1/16-1/8″. The first power trowel pass is considered the ‘floating pass’, is done at a slow uniform pace, and typically utilizes floating blades. Troweling commonly begins at the top of the slab and moves from side to sides with the operator moving backwards eliminating foot traffic imperfections (also passing over the forms to promote level joints). On the floating pass, the trowel blades are commonly flat creating a suction between the concrete and blade. Faint circular marks are usually left on the surface and will be removed on the next pass. After the floating pass is complete the finish pass is usually done (after surface is dry and walking leaves no impressions) and finish blades are used on the trowel. A good rule of thumb for starting finish trowel operations is when the operator places his hand on the surface and no sand or cement is left as residue. For the finish pass the angle of the blades is increased to approximately 5-10 degrees. Many passes with increasing blade angles may be necessary and the higher the blade angle the harder the finish.
Broom – The broom pass is made after the float pass and after the surface hardens enough to not be marred by the weight of the broom. Brooms may be attached to extension poles or handheld. Pole mounted units are most commonly available in 2′, 3′, 4′, 6′, and 8′ widths. Also new handless rope driven brooms have become popular and can increase efficiency and productivity.
