
mortar
Mortar is commonly used in masonry as the rigid joint material between masonry units and is a mix of sand, cement, lime, and water. It is used for several reasons: cushions units for bearing against one another, seals between the units from water and wind, bonds units into a monolithic system, and is important to the aesthetic appearance of the wall. Lime is added to increase workability and smoothness to the mortar. Blended Hydraulic Cements (pozzolan subsidized) ASTM C270 is a common testing spec with respect to masonry mortar. There are 3 types of mortar mixes for masonry wall construction:
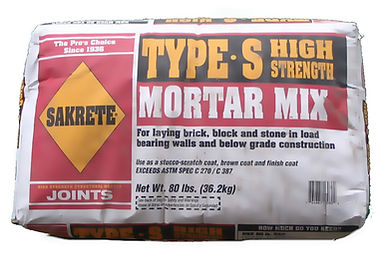

- Bagged/premixed Mortar Cement (standard formulations – cement/lime mortar) achieves a better bond strength between unit and mortar, is often not air entrained, has higher flexural and shear strength of wall system compared to Masonry Cement. Many premixed mortar bag products come in 80lb bags and will require addition of sand and water on site. Some products available will have the sand included in the bag mixture, but this is often less economical and less practical for projects requiring larger mortar quantities.
- Site mixed Portland Cement, Lime, and Sand
- Bagged/premixed Masonry Cement (proprietary formulations) lessened bond strength between unit and mortar, often air-entrained, has reduced flexural and shear strength of wall system compared to standard Mortar Cement.
Site mixed mortar is the traditional preference for mortar but because of human input variations, it can have variations in mix and color. The types of mortar are as follows:
Type M – Commonly used below grade, hih strength, 2500PSI. Has less workability than Type S or N mortars. Commonly used with load bearing masonry work, chimneys, and brick manholes. Initially sets in approximately 1-1/2 hours, final set in 24 hours. Typically +/-1800psi in 7 days, +/- 2500psi in 28 days. Commonly 1 part cement, 1/4 hydrated lime, and 3 parts sand.
Type S – Commonly used at or below grade, medium strength, high tensile bond strength, 1800PSI. Higher flexural bond strength than Type N. Most commonly seen as used with brick pavement and patios, sewers, retaining walls, brick manholes, foundation walls. Initially sets in approximately 1-1/2 hours, final set in 24 hours. Typically +/-1300psi in 7 days, +/- 1800psi in 28 days.
Type N – Most commonly used unless there is a specific reason to choose another mortar, balance of good bonding capabilities and workability. general purpose mortar mix used above grade in interior and exterior applications. Initially sets in approximately 2 hours, final set in 24 hours. Typically +/-500 psi in 7 days, +/- 800psi in 28 days. Commonly 1 part cement, 1 part lime, and 6 parts sand.
Type O – Lime righ mortar which is commonly used as ‘pointing mortar’. Common strength is 350psi

Mortar will typically need to be 10-12% air entrained to effectively resist freeze thaw temperatures. Cement to Sand proportions for job mixed mortar are commonly in the range of 1:2-1/4 to 1:3-1/2 but will depend on job specific specifications assigned by the engineer. Machine mixing is more efficient and consistent in terms of mixes. It is common for the water and half the sand be added, followed by the masonry cement and the rest of the sand, then the rest of the water is added. The final water is added after one minute of continuous mixing. Mixing should be continued for 3 to 5 minutes. Mortar may stiffen and still be retempered with water is it was mixed less than 90 minutes prior. Any more than 2-1/2 hours old and the mortar should be discarded as it has already begun to rehydrate. Mortar in small amounts can be mixed in a bucket or wheelbarrow.
Mortar quantities in moderate amounts can be mixed in large buckets or a mortar tub with mechanical mixing devices, paddles, mixers etc.



For any substantial quantities mortar will often be mixed in a towable mortar mixer gas (or electric) powered unit. These towable units have varying capacities based on manufacturer but often carry +/- 6 cubic feet of material. Larger units can carry up to 9 cubic feet however. Mortar pumps may be utilized which often receive mixed mortar directly from the mixer and pump the mortar through a hose exactly to the designated area where the mortar is needed. This allows the mortar materials and mixing operation to be held to one location on site.
The more common joint thickness is 3/8″ but 1/4″ and 1/2″ joints are also used. After the bricks/blocks and/or bed joint of the previous joint are ‘buttered’, and each successive row of units are placed and leveled, the joints will often be ‘struck-off’ or ‘tooled’ for a cleaner, more appealing look. Then the joints are brushed for a final cleaning.


Appropriately placing mortar consists of head and bed joint filling, careful unit placement, joint tooling, weather considerations, and cleaning. Mortar should be kept at a temperature of 40 degrees fahrenheit or above at all times
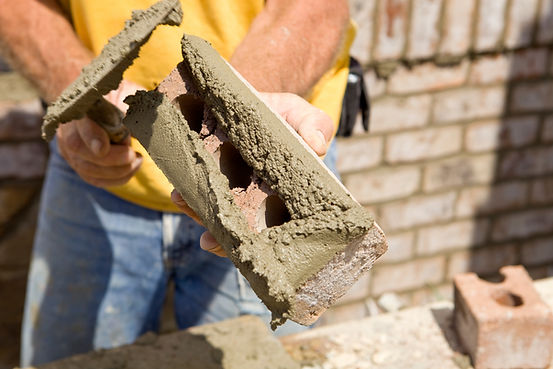
There are several joint types available:
-Concave
-V
-Grapevine
-Weathered
-Beaded
-Struck
-Flush
-Raked
-Extruded





