
asphalt placement
Asphalt is made up of heated asphalt cement or binder, mineral filler (limestone dust, Portland cement, etc), and aggregate. The fundamental concept of a pavement section is a suitable subgrade, a compacted aggregate base, an asphalt base course (if required), an intermediate course, and a surface course. Asphalt base, intermediate, and surface courses have reduced aggregate gradation sizes respectively driven by the need to provide a proper successive foundation for traffic loading. Base courses are rough but strong in nature, intermediate (or leveling) course provides the needed improvement in localized peaks and valleys, and surface course provides the final smooth substrate for traffic.
Asphalt mixes are commonly grouped in three traffic ‘types’, heavy, medium, and light which are driven by many factors, aggregate gradation and asphalt binder content being the more significant. “Fine” particle content (75 micrometers to 4.5 millimeters) makes up a relatively small portion of asphalt mixtures, typically 30% or less of the total aggregate content.
Asphalt binder is a viscous hydrocarbon produced by residue produced by the petroleum distillation process. Binder content commonly makes up 25-30% of asphalt mix cost, depending on the mix. The most commonly used grading system today is the ‘Superpave’ ‘performance grade’ system which utilizes a temperature range, supported by laboratory performance testing. Example: 64-22, where 64 degree fahrenheit represents the average 7-day max pavement temperature, and -22 makes up the expected minimum pavement temperature anticipated. Also, asphalt cement binder ‘polymer’ modifiers have become popular in the last 10-20 years as they can increase overall performance of the mix over time in relation to the added cost. Asphalt binder is also graded by some in viscosity, most commonly represented at AC-10, AC-20, AC-30, AR-4000.
Surface lifts of asphalt typically have aggregate particles ranging up to just under 1/2″ and +/- 3/8″ (medium and light duty). Asphalt binder content for surface lifts is commonly between 5-10% of the mix volume.’Virgin’ asphalt binder content is commonly required in asphalt surface courses (except heavy duty types) at a minimum of 5% of the total mix volume. RAP (Recycled Asphalt product) is typically permitted in new surface course asphalt mixes in the amount of 10% (heavy duty mix) or 20% (light or medium duty mix).
Intermediate lifts of asphalt typically have aggregate particles ranging up to just under 1-1/2″ and 1″ (medium and light duty) with binder content ranges of 4-9%. Virgin asphalt binder is commonly required in intermediate course asphalt mixes at a minimum of 3% of the total mix volume. RAP (Recycled Asphalt product) is typically permitted in new intermediate course asphalt mixes in the amount of 35% of the total mix volume. Most engineers will not allow intermediate lifts of asphalt to be placed in excess of 3″ at a time.
Base lifts of asphalt typically have aggregate particles ranging up to just under 2″ with binder content ranges of 2-6% of the total mix volume. Virgin asphalt binder is commonly required in base course asphalt mixes at a minimum of 1-2% of the total mix volume. RAP (Recycled Asphalt product) is typically permitted in new base course asphalt mixes in the amount of 40-50% of the total mix volume. Most engineers will not allow base lifts of asphalt to be placed in excess of 6″ at a time.
At the asphalt plant the aggregate/mineral mixture is formulated accurately in the hopper and then the binder is added at the appropriate rate and mixed thoroughly together before being released through the bottom end of the hopper into the hauling truck.

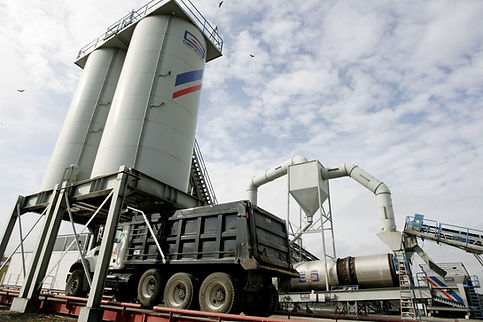
The hauling truck’s bed is commonly sprayed with release agent to prevent sticking of the mixture. A cover is required over the top of the bed to trap in heat and to keep wind and rain from entering the bed and mixture. The amount of asphalt a truck can carry is based more on truck weight ratings and local jurisdictions more than actual volumetric capacity of the truck bed. For example, a quadruple axle truck will commonly be rated to haul approximately 17-19 Tons (8.5-9.5 Cubic Yards).
Enough trucks will be required to place hot asphalt mix into the paver or spreading equipment’s hopper consistently to keep the equipment in constant motion and hot. The number of trucks required is dependent on the location of the asphalt mixing plant, the size of the truck bed, local traffic conditions, the area to be covered, and the amount of asphalt mix to be placed. A small paving operation may only need 1-3 trucks while a large mainline road paving operation can require as much as 4-6 trucks or more. Haul routes will sometimes need to be planned out in advance of paving operations to assure the engineer or locality will approve of road/bridge load limit guidelines and any asphalt binder tracking that might occur due to tires. A logical and efficient location must be established for trucks to wait for their turn in hopper placement and for the actual act of placement into the hopper. This process must all be organized and planned to minimize interference and disruption to passing and local traffic.

Prior to asphalt placement the existing surface asphalt surface will need to be clean and dry to promote adhesion of tack/prime coat and subsequent asphalt lifts being placed. The cleaning operation is commonly done with a sweeper truck or tractor. Also, liquid asphalt will typically be required by way of a separate spot nozzle typically attached to a hot kettle trailer. This liquid is applied on most all of the areas perimeter, i.e. curbs, butt joints, etc (and sometimes cold joints) to promote adhesion and seal against moisture penetration (which can lead to unwanted freeze-thaw and eventual deterioration).

Prime coat is commonly used on stone or concrete base to promote base adhesion, limit capillary moisture action upwards into asphalt lift, and to provide a more durable base if imminent paving isn’t expected. Tack coat is used between the intermediate and surface courses and promotes adhesion and a good bond between two lifts of asphalt. Typically the asphalt truck will be connected to and towed/pushed forward by the paver at the desired speed. The asphalt is then released from the hopper into the conveyor/spreader and on to the preheated screed to be placed in the appropriate lift and cross slope. (See Asphalt Paver Operation).
Placement and compaction are the most important factors in installation of successful asphalt pavement performance. Asphalt is placed in ‘lifts’ which are typically at least 3 times the thickness of the maximum aggregate size.+/- 3-10″ is common for asphalt bases, 1-3/4″ – 3″ for intermediate courses, and 1-1/4″ – 2″ for surface course, though other thicknesses are possible for special situations or asphalt product types. The purpose of installing asphalt in lifts is to avoid mat tearing, which typically looks like longitudinal streaks.
Compaction is considered by many, the greatest determined factor in dense-graded asphalt pavement performance. Compaction is measured by density or ‘percent air voids’ information which is gathered by testing operations. The two common testing methods are:
-on site extraction of pavement cores which are tested in the lab (most accurate but also very resource intensive and costly)
-nuclear or electrical density gauge
A rule of thumb used by some is for every 1% increase in air content that’s above the 6-7% accepted maximum, pavement life can be reduced by up to 10%. The common air content range for dense-graded asphalt mixes is 3-8%. Poor compaction can lead to a host of problems: decreased durability, raveling, rutting, freeze/thaw moisture damage, reduced fatigue life, reduced stiffness, etc.
The largest factor affecting compaction is considered by many to be asphalt mix temperature at placement. The reason for this is because of the amount of time provided in the ‘window of compactive effort’ where the temperature is at or near peak (usually 250F for Hot Mix, 290F for many modified binders mixes). Too soon and the roller will ‘roll’ the mix. Too late and the mix will be too cold to receive compaction efforts. Many consider a conducive temperature for compaction (dense-graded mixes) to be between above 230 degrees fahrenheit. The ‘cessation’ temperature is commonly around 175 degrees Fahrenheit at which point compactive efforts become inefficient. After this point rollers can still improve smoothness and surface texture, but further compaction will commonly cease. It’s important to note that thicker lifts of asphalt stay warmer longer, however ambient temperature, wind, and and sun play a significant role in peak maintenance of mix temperature. Other factors that can affect compaction are mixture (aggregate properties, binder properties/amount) and installation (roller properties/number, haul, base).
A common rule of thumb used in the field is final compacted asphalt will lose 1/4″ per inch of design lift thickness, so the screed depth is adjusted accordingly. Example; a design 2″ lift of intermediate course, will require an approximate screed depth of 2-1/2″.
Once the asphalt is placed into the desired lift thickness and while the asphalt is still hot, steel wheel and pneumatic type rollers will make several (often as much as 5-10 times or more depending many factors) passes across the asphalt surface to achieve maximum final material placement density. Vibratory rollers have become rather popular as they often provide a better compaction result than static rolling. However they also require a higher degree of operator control, and must be used with caution in residential areas, areas with fragile utilities, etc. Amplitude and frequency can be adjusted for on vibratory rollers, which maximize compactive effort. In general when using vibratory rollers, higher frequencies and lower roller speeds are ideal because they increase compactive effort and provide a smoother mat. 2.5″ and greater lifts will commonly use high frequency high amplitude more (along with stiff mixes). Lifts between 1.5 and 2.5″ will typically use high frequency low amplitude mode. And thin lifts less than 1.25″ typically operated in static mode only (to reduce shoving or aggregate crushing). For most standard mix types and lift thicknesses, low-amplitude/several pass approach is common.
A ‘breakdown’ roller (vibratory smooth or pneumatic roller) is utilized first and commonly travels 2-3 mph and operates as close to the paver as possible. An ‘intermediate’ roller (typically smooth drum but sometimes pneumatic) is used second and typically travels 2.5-4 mph. A ‘finish’ roller (typically smooth drum static roller) is used at the end and usually runs from 3-7 mph. Thin lifts (1.25″ and smaller) should not receive vibratory compaction as shoving, displacement, and aggregate fracturing can occur. Also a small or ‘peanut’ roller may be used to trim out edges, corners, or hard to reach areas. Most rollers range in width between 3-7′. Many modern steel wheel rollers can be ballasted with sand or water. Rollers should never be stopped on a fresh mat as they can cause humps that are near impossible to fix.

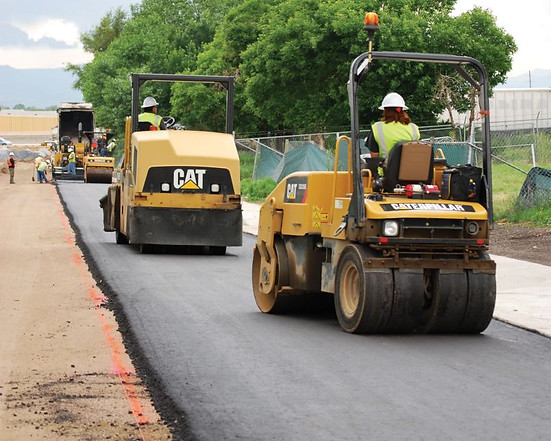
For pneumatic tired rollers, it’s important for the tire pressure to be correct for proper minimum contact area and contact pressure requirements. Pneumatic rollers provide a ‘kneading’ type action which improves compaction, applies more horizontal forces to the compaction effort, and rearranges the aggregate to increase the possibility of better compaction. The tires and wheels on the rollers are consistently moistened to prevent adhesion of the mixture.
It is common for asphalt base mixtures to be compacted with pneumatic and steel wheel rollers. It is common for intermediate and surface courses to utilize a steel wheel roller. Variable depth courses are commonly compacted with pneumatic and steel wheel rollers. For polymer asphalt mix, only steel wheel rollers should be used. Any surface deviations caused by the use of pneumatic rollers must be corrected with the steel wheel rollers.
Rollers typically start on the outside of the lane and make one complete pass. They will then move inward towards the crown of the road and overlap the previous pass by approximately 6″. Compaction is done until displacement of the asphalt occurs no more. For cold joints, it is a good idea to keep the rollers at least 12″ from the unsupported edge, until the adjacent lift is placed. It is common for longitudinal cold joints in successive lifts be staggered reducing the chance of significant joint separation, a key location for deterioration to occur. Any road ‘crowns’ should never be rolled over as they will become flattened.

Along curbs, around castings, and in other hard to reach areas, mix is placed then tamped with a hand or mechanical tamp. Handwork with an asphalt rake and/or shovel is almost always required. 1-3 laborer often follow along with the paver, fixing any minor inconsistencies in placement and placing asphalt in areas where the paver can’t reach (around castings, curb bumpouts, intersections, unusual radii, etc). handwork should be minimized as it’s subject to aggregate segregation and a rougher surface texture.

